5 important things you need to take a notice when designing a product-specific fixture with Blank System modules.
In the world of machining, precision is the key to success. Whether you’re a seasoned professional or a novice in the field, achieving accuracy in your workpieces is crucial.
In this article, we will talk about dedicated (product-specific) fixtures, but first, it is important to understand the difference between modular and dedicated fixture. We have been covered the differences between these two methods in our article How to use a modular workholding fixture.
1. The Foundation: Clamp Modules
At the heart of any robust fixture system are reliable clamping elements. When choosing the right workholding clamp for the fixture there are several things to consider, such as workpiece characteristics, machining force and machining area.
OK-VISE’s workholding clamps provide a strong and secure grip on workpieces, ensuring stability during machining processes. These modules are designed to handle a variety of materials and can generate a massive force within a small footprint (low-profile design). With OK-VISE clamp modules, you can rely on secure clamping for your fixture.
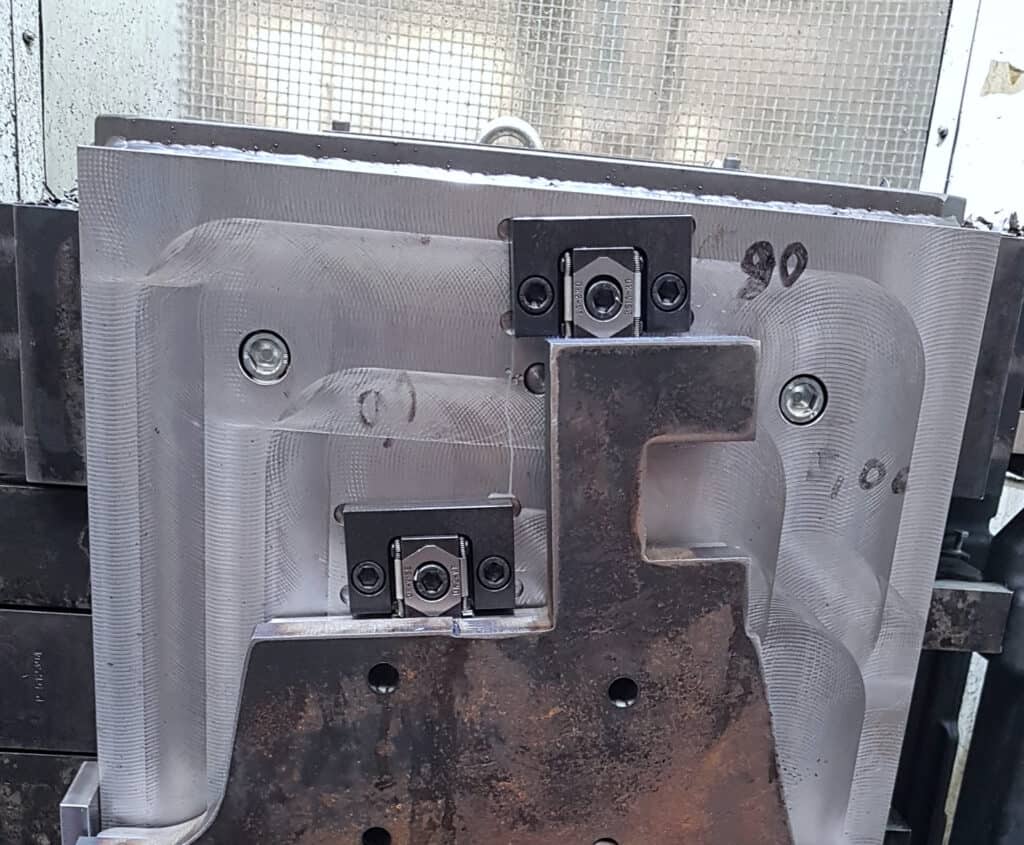
2. Precision in Locating: Stop Modules
Stop modules play a crucial role in achieving consistency and accuracy in machining. Like the workholding clamp, the features of the stop module must seamlessly complement the characteristics of the workpiece. Serving as a vital locating element in the fixturing process, the stop is required to exhibit strength and durability to ensure the consistency and repeatability of the fixture setup.
When we are talking about dedicated fixtures, there are basically two ways to implement the stop function. This function can be:
- Machined directly into the fixture plate. This method works well when machining is done from single direction, as in three-axis machining center.
- Built using stopper modules that are bolted to machined pockets (the “Blank System”). The workpiece can then be lifted from the base fixture plate to allow easier tool access in four- and 5-axis machining.
OK-VISE stop modules enable you to precisely locate and secure your workpieces. These modules are easy to install on the fixture plate using M12 bolts and are available in several different models, offering varying levels of friction and different jaw shapes.
3. Elevating Workpieces: Riser Blocks
In some machining applications, achieving the desired height for a workpiece is essential. This is usually the case when better access to the workpiece is needed or when making drillings into the workpiece.
Our Blank System riser blocks come into play in such scenarios. These blocks provide a stable and elevated platform for your workpiece, allowing you to access all angles and contours with ease.
4. Guiding Precision: Side Guides
Side guides are used to assist in locating the workpiece during the loading stage. Our Blank System side guides are installed in an M12 thread, where the upper part of the hole is used to locate the side guide accurately.
As stoppers, the side guide plays an important role in the 3-2-1 locating principle (also known as the six-point positioning principle), where the basic idea is that the workpiece has six degrees of freedom in space. To completely determine the position of the workpiece, it is necessary to eliminate these six degrees of freedom. The side guide will locate the workpiece side ways (in the picture above).
5. Machining Freedom: DIY Subplate or Ready-Made
The Blank System is based on the use of blank plates, such as aluminum or steel, which serve as a platform to build the fixture. OK-VISE understands that companies and machinists have different preferences and capabilities when it comes to subplates. Some may prefer to machine their subplates themselves, while others may opt for the convenience of ordering pre-made subplates. OK-VISE caters to both preferences, offering customers the freedom to decide how they want to approach this aspect of fixture assembly.
The Power of Customization
Our Blank System allows users to mix and match clamp modules, stop modules, riser blocks, and side guides to create a fixture tailored to their specific needs. The ability to customize the arrangement and combination of these components gives machinists the flexibility to address unique challenges posed by different projects.
Conclusion
Selecting OK-VISE components to build custom fixtures empowers machinists to elevate their precision game. The combination of clamp modules, stop modules, riser blocks, and side guides offers a comprehensive solution for achieving accuracy and consistency in machining operations. The flexibility to choose between machining a subplate in-house or opting for a pre-made one adds an extra layer of customization, catering to the diverse needs of machinists across different industries.
In the world of precision machining, where every micrometer matters, OK-VISE components stand out as reliable building blocks for workholding fixtures that meet the highest standards of accuracy and efficiency. Whether you’re working on complex prototypes or high-volume production runs, investing in a fixture system built with OK-VISE components is a step towards achieving machining excellence.
More information about the subject can be found here: Fixture design instructions.